A Comprehensive Guide To Automated Visual Inspection Of Lyophilized Vials
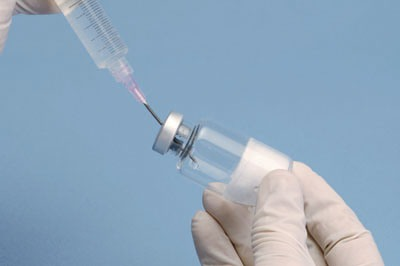
Table of Contents
Understanding Lyophilized Vials and Quality Control Needs
Lyophilization, or freeze-drying, is a crucial process for preserving pharmaceuticals and biologics, extending their shelf life and improving stability. The resulting lyophilized vials require rigorous quality control to ensure product integrity and patient safety. Visual inspection plays a vital role in this process.
- Lyophilization Applications: Preserving vaccines, pharmaceuticals, and biologics.
- Importance of Visual Inspection: Detects defects that may compromise product quality or sterility.
- Common Defects:
- Cracks in the vial
- Particulate matter within the vial
- Cake collapse
- Discoloration
- Fill level inconsistencies
- Regulatory Compliance: Meeting GMP (Good Manufacturing Practices) and USP (United States Pharmacopeia) guidelines is crucial. Automated systems help ensure consistent compliance.
Automated Visual Inspection Systems: Technologies and Capabilities
Several technologies power automated visual inspection systems for lyophilized vials. Each offers unique advantages and disadvantages:
- Machine Vision: Utilizes cameras and image processing algorithms to detect defects. Offers high speed and accuracy.
- Image Analysis: Advanced algorithms analyze images to identify and classify defects, improving detection sensitivity.
- Artificial Intelligence (AI): AI-powered systems learn from past inspections, continuously improving their accuracy and adapting to variations in vial appearance. This technology is especially useful for identifying subtle defects.
Key features of an effective AVI system:
- High-resolution cameras for detailed image capture.
- Advanced lighting techniques (e.g., structured lighting) to enhance defect visibility.
- Sophisticated algorithms for precise defect detection and classification.
- User-friendly software for easy operation, data management, and reporting.
Leading vendors: [Mention specific vendors and their relevant systems – this requires research and should be updated periodically to reflect the current market].
Implementing Automated Visual Inspection: A Step-by-Step Guide
Implementing an automated visual inspection system for lyophilized vials involves several key steps:
- Needs Assessment: Define specific inspection requirements and identify critical defects.
- System Selection: Choose a system that meets your needs in terms of speed, accuracy, and throughput.
- System Integration: Seamlessly integrate the AVI system with existing production lines and quality control workflows.
- System Validation and Qualification: Ensure the system performs accurately and reliably. This involves IQ (Installation Qualification), OQ (Operational Qualification), and PQ (Performance Qualification).
- Operator Training: Train personnel on system operation, maintenance, and data interpretation.
- Data Management and Reporting: Implement robust data management processes to ensure traceability and compliance with regulatory requirements. This often involves integrating the system with existing LIMS (Laboratory Information Management System) or ERP (Enterprise Resource Planning) systems.
Benefits and ROI of Automated Visual Inspection
Automated visual inspection offers significant benefits compared to manual methods:
- Improved Efficiency: Increased throughput and reduced inspection time.
- Reduced Labor Costs: Fewer human inspectors are needed.
- Enhanced Accuracy: Minimized human error leading to more consistent and reliable results.
- Minimized Risks: Reduced potential for human error resulting in fewer quality defects reaching the market.
- Improved Compliance: Supports adherence to GMP and other regulatory requirements.
ROI: The return on investment depends on various factors, including the initial system cost, labor savings, reduced waste, and improved product quality. A detailed cost-benefit analysis should be conducted to accurately assess ROI for your specific situation.
Future Trends in Automated Visual Inspection of Lyophilized Vials
Several emerging technologies are shaping the future of automated visual inspection:
- Advanced Image Processing: More sophisticated algorithms for detecting even subtle defects.
- AI-Powered Defect Detection: AI and machine learning will improve detection accuracy and reduce false positives.
- Integration with Other QC Systems: Seamless integration with other quality control systems for a holistic approach to product quality.
- Increased Automation: Greater levels of automation throughout the entire inspection process, minimizing manual intervention.
Conclusion: Optimizing Lyophilized Vial Inspection with Automated Solutions
Automated visual inspection of lyophilized vials is no longer a luxury but a necessity for pharmaceutical and biotech companies striving for efficiency, accuracy, and regulatory compliance. By transitioning from manual to automated methods, businesses can significantly reduce costs, improve product quality, and mitigate risks. Invest in automated visual inspection of lyophilized vials today to enhance your quality control processes and ensure the safety and efficacy of your products. Learn more about optimizing your lyophilized vial inspection with automated solutions and take the next step towards enhanced quality control.
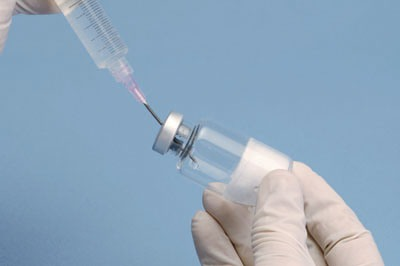
Featured Posts
-
Pritchard Named Nba Sixth Man Of The Year
May 11, 2025 -
Global Sea Level Rise Implications For Coastal Development
May 11, 2025 -
Debbie Elliott Biography And Career Highlights
May 11, 2025 -
The Los Angeles Wildfires A Growing Market For Disasters Bets
May 11, 2025 -
Lily Collins Sizzling New Calvin Klein Ads
May 11, 2025