Automated Visual Inspection Of Lyophilized Vials: Challenges And Solutions
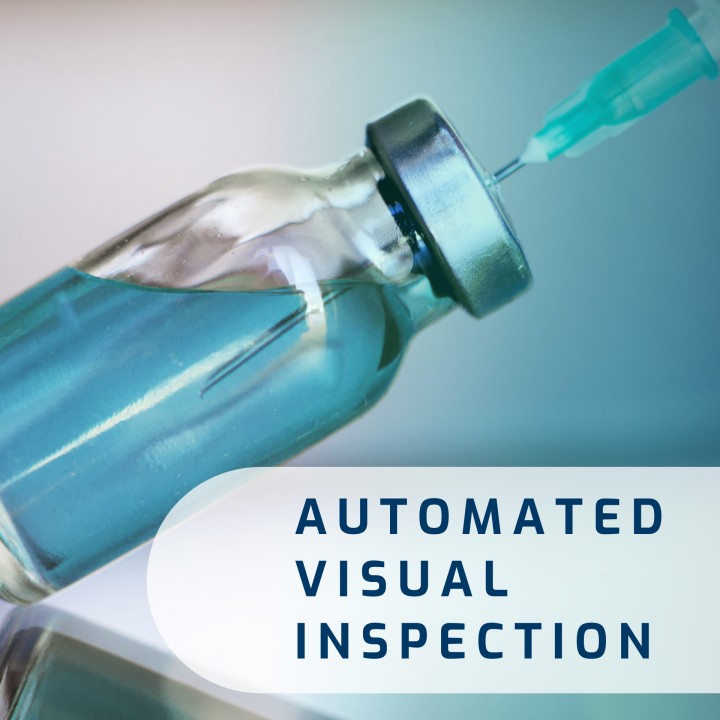
Table of Contents
Challenges in Automated Visual Inspection of Lyophilized Vials
Automated visual inspection of lyophilized vials presents several significant hurdles. Achieving consistent and accurate defect detection requires overcoming inherent variations in the lyophilization process itself and the complexities of identifying subtle defects. Furthermore, the high-throughput demands of pharmaceutical manufacturing add another layer of complexity.
Variations in Lyophilization Processes
Lyophilization, or freeze-drying, is a complex process, and variations in cycle parameters can significantly impact the final product's appearance. These variations make consistent automated defect detection challenging.
- Inconsistent Cake Appearance: Different lyophilization cycles can result in variations in the appearance of the lyophilized cake, including differences in texture, density, and color. This variability makes it difficult for automated systems to consistently identify defects.
- Vial Filling and Stopper Seating: Variations in vial filling levels and stopper seating can affect image analysis algorithms. Inconsistent filling can create shadows or reflections that interfere with defect detection, while improperly seated stoppers can lead to false positives.
- Need for Robust Algorithms: Automated visual inspection systems require robust algorithms capable of handling the inherent variability in lyophilized vials. These algorithms must be adaptable and able to compensate for variations in lighting, background, and vial geometry.
- Importance of Image Pre-processing: Effective image pre-processing techniques are crucial to reduce noise and artifacts that can interfere with defect detection. These techniques might include noise filtering, background correction, and image enhancement.
Complex Defect Identification
Detecting subtle defects in lyophilized vials is a major challenge. These defects can include cracks in the lyophilized cake, particulate matter within the vial, discolorations, and other irregularities that might not be readily apparent to the naked eye.
- Subtle Defects: Identifying subtle defects like minute cracks, small particles, and slight discolorations requires advanced image processing techniques and sophisticated algorithms.
- Distinguishing Acceptable Variations from Critical Defects: One of the biggest challenges is differentiating between acceptable variations in the lyophilized cake and critical defects that could compromise product quality or safety. This requires careful consideration of acceptance criteria and the development of robust classification algorithms.
- High-Resolution Imaging: High-resolution imaging systems are essential for capturing the fine details necessary for accurate defect detection. This is particularly important for identifying small particles or subtle cracks in the lyophilized cake.
- AI-Powered Solutions: The use of AI and machine learning is crucial for improving the accuracy and speed of defect classification. These advanced techniques allow the system to learn and adapt to variations in the appearance of lyophilized vials over time.
High Throughput Requirements
Pharmaceutical manufacturing lines require high-speed inspection to maintain productivity and meet demand. Balancing the speed of inspection with the accuracy of defect detection is a considerable challenge.
- High-Speed Cameras: High-speed cameras are essential for inspecting vials at the required throughput rates. These cameras must be capable of capturing high-quality images at speeds that keep pace with the production line.
- Parallel Processing: Parallel processing capabilities are often necessary to handle the large volume of image data generated during high-speed inspection. This ensures that the inspection process doesn't become a bottleneck in the manufacturing line.
- Real-Time Defect Detection: Efficient algorithms are needed for real-time defect detection. These algorithms must be able to process images quickly and accurately, without sacrificing detection sensitivity.
- Minimizing Downtime: System reliability is paramount to prevent costly downtime on the production line. Robust design and preventative maintenance are key factors in achieving this goal.
Solutions for Automated Visual Inspection of Lyophilized Vials
Overcoming the challenges of automated visual inspection requires a multi-pronged approach, leveraging advanced imaging technologies, the power of artificial intelligence, and the integration of inspection systems into the broader manufacturing process.
Advanced Imaging Technologies
The use of advanced imaging technologies significantly improves the visibility and detectability of defects in lyophilized vials.
- High-Resolution Cameras and Specialized Lighting: High-resolution cameras, coupled with optimized lighting techniques such as structured lighting or polarized light, enhance the visibility of subtle defects.
- Multi-spectral Imaging: Multi-spectral imaging techniques can detect defects that are not visible in the visible spectrum, providing a more comprehensive inspection. This is particularly useful for detecting subtle variations in color or texture.
- Hyperspectral Imaging: Hyperspectral imaging, a more advanced form of multi-spectral imaging, offers even greater detail and sensitivity, allowing for the detection of a wider range of defects.
- 3D Imaging: 3D imaging techniques provide a more complete representation of the vial and its contents, facilitating the detection of defects that might be missed by 2D imaging alone.
Artificial Intelligence and Machine Learning
AI and machine learning algorithms are transforming the field of automated visual inspection by enabling more accurate and efficient defect detection.
- AI-powered Defect Identification: AI algorithms can be trained to identify complex defects with high accuracy, surpassing the capabilities of traditional image analysis methods.
- Deep Learning Models: Deep learning models, such as convolutional neural networks (CNNs), are particularly well-suited for image classification tasks and can achieve high levels of accuracy in identifying defects in lyophilized vials.
- Transfer Learning: Transfer learning techniques can accelerate model training by leveraging pre-trained models and adapting them to the specific characteristics of lyophilized vial inspection.
- Continuous Learning: The ability of AI systems to learn and adapt over time through continuous learning ensures that the inspection system remains accurate and effective even as variations in the lyophilization process occur.
Integrated Inspection Systems
Integrating inspection systems seamlessly into existing manufacturing lines is crucial for efficient and effective operation.
- Seamless Integration: Integration with existing manufacturing execution systems (MES) and other automation systems ensures that inspection data is seamlessly incorporated into the overall production process.
- Real-Time Data Analysis and Reporting: Real-time data analysis and reporting provide immediate feedback on product quality, allowing for prompt identification and correction of any issues.
- User-Friendly Interfaces: User-friendly interfaces make the system easy to operate and maintain, minimizing downtime and maximizing efficiency.
- Data Analytics for Process Optimization: Data analytics tools can be used to identify trends and patterns in defect rates, providing valuable insights for optimizing the lyophilization process and improving overall product quality.
Conclusion
Automated visual inspection of lyophilized vials is critical for ensuring product quality and patient safety within the pharmaceutical industry. While challenges exist in managing process variability and identifying subtle defects, advancements in imaging technologies, AI, and system integration are providing increasingly effective solutions. By adopting these innovative approaches, pharmaceutical manufacturers can enhance the accuracy, speed, and efficiency of their inspection processes, leading to superior product quality and reduced risks. Investing in advanced automated visual inspection systems for lyophilized vials is a necessity for maintaining competitiveness and ensuring patient safety. Explore the latest advancements in automated visual inspection of lyophilized vials today!
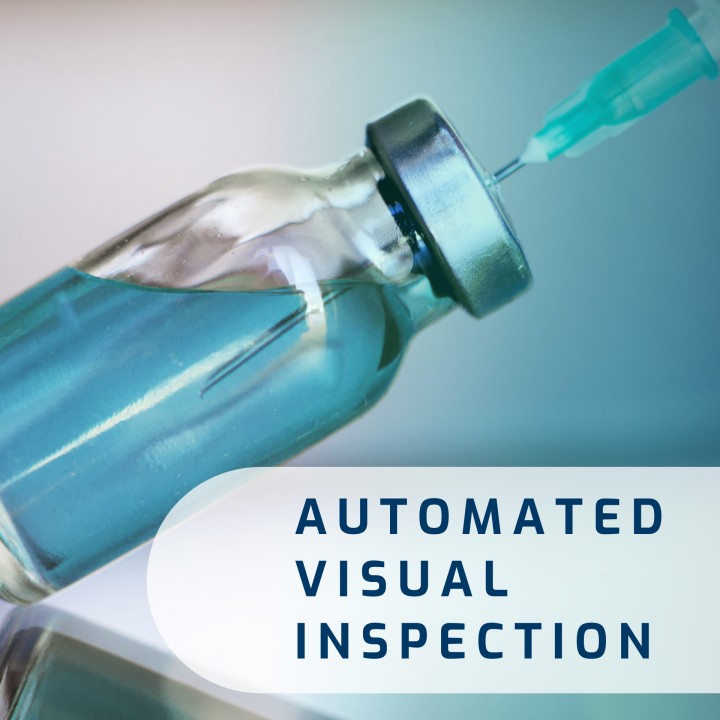
Featured Posts
-
Ofitsialno Antoan Baroan V Ludogorets
May 11, 2025 -
Saisonende Bundesliga Abstieg Fuer Bochum Und Kiel Leipzig Ohne Champions League
May 11, 2025 -
The Michael Kay Juan Soto Aaron Judge Dynamic A Baseball Analysis
May 11, 2025 -
Injury Concerns For Yankees And Brewers Series March 27 30
May 11, 2025 -
Filming In Uruguay A Comprehensive Guide For International Productions
May 11, 2025