Efficient Automated Visual Inspection Of Lyophilized Vials: Addressing Key Challenges
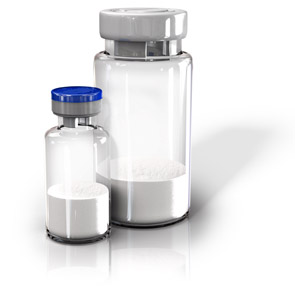
Table of Contents
Overcoming the Limitations of Manual Inspection
Manual visual inspection of lyophilized vials presents several significant drawbacks that impact both efficiency and product quality.
High Labor Costs and Time Constraints
Manual inspection is a labor-intensive process, leading to substantial costs. These costs encompass not only labor wages but also extensive training for inspectors to maintain consistent standards and the overhead of supervision.
- Increased labor costs due to higher wages and benefits for skilled inspectors.
- Significant time investment in comprehensive training programs to ensure consistent inspection quality.
- Potential production delays and increased costs due to staff shortages or absenteeism.
- Automated systems can reduce labor costs by up to 70%, freeing up personnel for other critical tasks. The return on investment (ROI) is typically realized within 12-18 months.
Subjectivity and Variability in Human Inspection
Human inspectors, despite training, are susceptible to fatigue, leading to inconsistencies in their assessment of defects. Subjective interpretations of what constitutes a “defect” can lead to variations in inspection results.
- Fatigue-related errors leading to missed defects or false positives.
- Inconsistent interpretation of visual defects across different inspectors.
- Variations in inspection standards leading to inconsistent results.
- Automated systems eliminate subjective interpretation, ensuring consistent and objective assessment of each vial. This significantly reduces the risk of human error and improves overall product quality.
Bottlenecks in Production Throughput
Manual inspection often becomes a significant bottleneck in the production process, limiting overall throughput and efficiency. The speed of manual inspection is inherently limited, impacting the overall production capacity.
- Manual inspection can reduce production throughput by as much as 50% compared to automated systems.
- Automated systems significantly increase production capacity, reducing lead times and improving overall efficiency.
- The higher throughput allows for faster delivery of products to market, enhancing competitiveness.
Key Features of Efficient Automated Visual Inspection Systems
Automated visual inspection systems leverage advanced technologies to overcome the limitations of manual methods.
High-Resolution Imaging and Advanced Algorithms
These systems employ high-resolution cameras with specialized lighting to capture detailed images of each lyophilized vial. Sophisticated algorithms, including image processing and machine learning techniques, then analyze these images to detect defects.
- High-resolution cameras capture even subtle defects, improving detection sensitivity.
- Specialized lighting techniques enhance contrast and visibility of defects.
- Advanced algorithms, such as convolutional neural networks (CNNs), are trained to identify specific defect types with high accuracy.
- Machine learning algorithms continuously learn and improve their detection capabilities over time, reducing false positives and improving accuracy.
Automated Defect Classification and Reporting
Automated systems automatically categorize detected defects based on pre-defined criteria. This detailed information is then compiled into comprehensive reports, providing valuable data for quality control and analysis.
- Automated classification of defects such as particulate matter, cracks, discoloration, and cake inconsistencies.
- Detailed reports provide data traceability, facilitating efficient root cause analysis and process improvements.
- Automated reporting streamlines quality control processes, reducing manual documentation and improving efficiency.
Integration with Existing Production Lines
Modern automated systems are designed for seamless integration into existing production lines, minimizing disruption and maximizing efficiency. This ensures smooth transition and minimal downtime during system implementation.
- Modular designs allow for flexible integration with various production line configurations.
- Integration with existing data management systems ensures seamless data flow and traceability.
- Minimizing downtime during system implementation is crucial for maintaining production schedules.
Addressing Specific Challenges in Lyophilized Vial Inspection
Lyophilized vials present unique inspection challenges due to the inherent variability in the appearance of the lyophilized cake.
Dealing with Variations in Lyophilized Cake Appearance
Variations in cake appearance, such as color, texture, and density, can complicate defect detection. However, advanced algorithms can compensate for these variations and improve accuracy.
- Sophisticated algorithms utilize image processing techniques to normalize variations in cake appearance.
- Machine learning models are trained on diverse datasets representing various cake appearances to improve robustness.
Minimizing False Positives and Ensuring Accuracy
Minimizing false positives while maintaining high accuracy is crucial for efficient automated inspection. Quality control measures, such as statistical process control (SPC), are used to ensure reliability.
- Stringent quality control procedures are implemented to minimize false positive rates.
- Automated systems offer significantly higher accuracy rates compared to manual inspection, often exceeding 99%.
Compliance with Regulatory Requirements
Automated visual inspection systems are designed to ensure full compliance with stringent regulatory requirements for pharmaceutical manufacturing, such as FDA and GMP guidelines.
- Automated systems provide detailed documentation of inspection processes, facilitating audits and regulatory compliance.
- Data traceability and reporting features enhance compliance with regulatory requirements.
Conclusion: The Future of Efficient Automated Visual Inspection of Lyophilized Vials
Efficient automated visual inspection of lyophilized vials offers significant advantages over manual methods. It increases efficiency, improves accuracy, reduces labor costs, and minimizes the risk of human error. By addressing the challenges of subjectivity, high labor costs, and throughput limitations, automated systems ensure superior product quality and compliance with stringent regulatory requirements. Invest in efficient automated visual inspection of lyophilized vials today to enhance your manufacturing processes and ensure superior product quality.
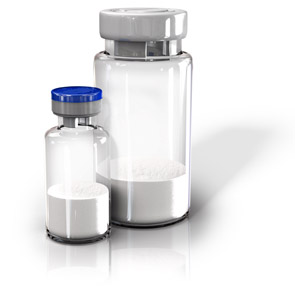
Featured Posts
-
Jeremy Stephens Shocking Return To The Ufc Fan Reactions
May 12, 2025 -
Sylvester Stallone One Film He Directed But Didnt Star In And Why It Failed
May 12, 2025 -
Afstemning Aben Dansk Melodi Grand Prix 2025
May 12, 2025 -
Seleccion Colombia En Vivo Uruguay Vs Colombia Sudamericano Sub 20
May 12, 2025 -
Asylum Minister Faber Survives No Confidence Motion In Parliament
May 12, 2025