Improving Automated Visual Inspection Of Lyophilized Vials: A Practical Guide
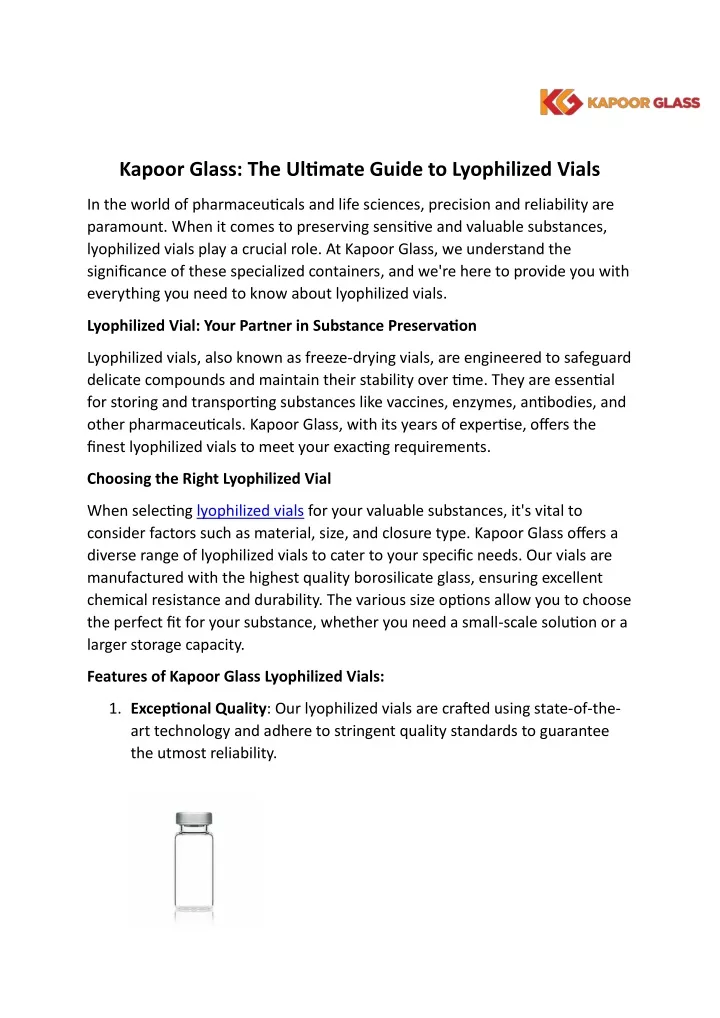
Table of Contents
Enhancing Image Acquisition for Improved Accuracy
High-quality image acquisition is fundamental to successful automated visual inspection. Subtle defects in lyophilized vials, such as cracks, particulate matter, or discoloration, can be easily missed with inadequate imaging. Optimizing lighting and camera settings is crucial for capturing clear, detailed images that facilitate accurate defect detection.
Optimizing Lighting and Camera Settings
Proper illumination is key to revealing even the smallest defects. Different lighting techniques offer unique advantages:
- Structured Light: Provides excellent surface detail and highlights subtle variations in height or texture.
- Coaxial Illumination: Minimizes shadows and reflections, ideal for inspecting transparent or translucent vials.
- Diffuse Lighting: Offers even illumination but may not reveal subtle surface imperfections as effectively.
Camera selection is equally important. Consider the following:
- High Resolution: Crucial for capturing fine details and resolving small defects.
- High Sensitivity: Enables clear images even with low light levels, crucial for delicate vials.
- Color Depth: Important for detecting subtle color variations indicative of defects.
Consistent illumination across all vials is vital to minimize shadowing and reflections, which can mask defects and lead to false negatives. Calibration procedures should be implemented to ensure uniform lighting and image acquisition across the entire inspection process.
Addressing Common Image Artifacts
Glare, reflections, and shadows are common image artifacts that hinder accurate defect detection. Strategies to mitigate these issues include:
- Noise Reduction Algorithms: Reduce image noise to improve clarity and contrast.
- Contrast Enhancement: Improves the visibility of defects by enhancing the difference between vial features and background.
- Specialized Filters: Can be used to reduce glare and reflections.
- Pre-processing Steps: Image preprocessing techniques like background subtraction can improve defect detection.
Careful calibration procedures ensure consistent image quality, minimizing the impact of variations in lighting, camera position, and vial orientation.
Advanced Algorithms for Defect Detection
Traditional image processing techniques may struggle to identify subtle defects. The application of advanced algorithms, particularly those based on machine learning and AI, significantly enhances the sensitivity and accuracy of automated visual inspection.
Machine Learning and AI for Enhanced Sensitivity
Machine learning algorithms, particularly deep learning and convolutional neural networks (CNNs), offer significant advantages:
- Deep Learning: Excellent at identifying complex patterns and subtle defects that might be missed by human inspectors or simpler algorithms.
- Convolutional Neural Networks (CNNs): Highly effective in processing image data, identifying and classifying defects with high accuracy.
Training these algorithms requires large datasets of images with accurately labeled defects. The quality and diversity of the training data directly impact the accuracy and robustness of the inspection system. Furthermore, AI-powered systems can self-learn and adapt to variations in vial types, fill levels, and defect characteristics, improving performance over time.
Implementing Robust Defect Classification
Accurate defect classification is essential for taking appropriate actions. Common defects in lyophilized vials include:
- Particulate Matter: Visible particles within the vial.
- Cracks: Fractures in the vial glass.
- Discoloration: Changes in the color or appearance of the lyophilized product.
- Fill Level Issues: Insufficient or excessive product in the vial.
Establishing clear criteria for defect classification and implementing automated reporting and data analysis tools ensures consistent and efficient processing of inspection results.
System Integration and Validation
Successful implementation requires seamless integration with existing production lines and adherence to stringent regulatory requirements.
Seamless Integration with Existing Production Lines
The automated visual inspection system should integrate smoothly with automated filling lines and other manufacturing equipment. This streamlined approach:
- Reduces Downtime: Minimizes interruptions to production.
- Improves Efficiency: Optimizes the overall manufacturing process.
Careful consideration of data transfer and communication protocols is essential for efficient integration and data management.
Validation and Compliance
Validation and qualification of automated visual inspection systems are crucial for regulatory compliance. This typically involves IQ/OQ/PQ (Installation Qualification, Operational Qualification, Performance Qualification):
- IQ: Verifies the system's proper installation and configuration.
- OQ: Confirms that the system performs as intended under specified conditions.
- PQ: Demonstrates that the system consistently meets performance requirements in a real-world setting.
Compliance with relevant regulations, such as FDA 21 CFR Part 11, requires meticulous documentation and ongoing performance monitoring. Regular system maintenance is crucial for ensuring long-term accuracy and reliability.
Conclusion
Improving the automated visual inspection of lyophilized vials involves a multifaceted approach encompassing optimized image acquisition, advanced algorithms, and robust system integration. By implementing the strategies outlined in this guide, pharmaceutical manufacturers can significantly enhance the accuracy, efficiency, and compliance of their inspection processes, leading to improved product quality and reduced risk. Optimize your automated visual inspection of lyophilized vials today. Invest in advanced automated visual inspection solutions for enhanced quality control and contact a reputable supplier to explore the latest technologies and find the perfect solution for your needs.
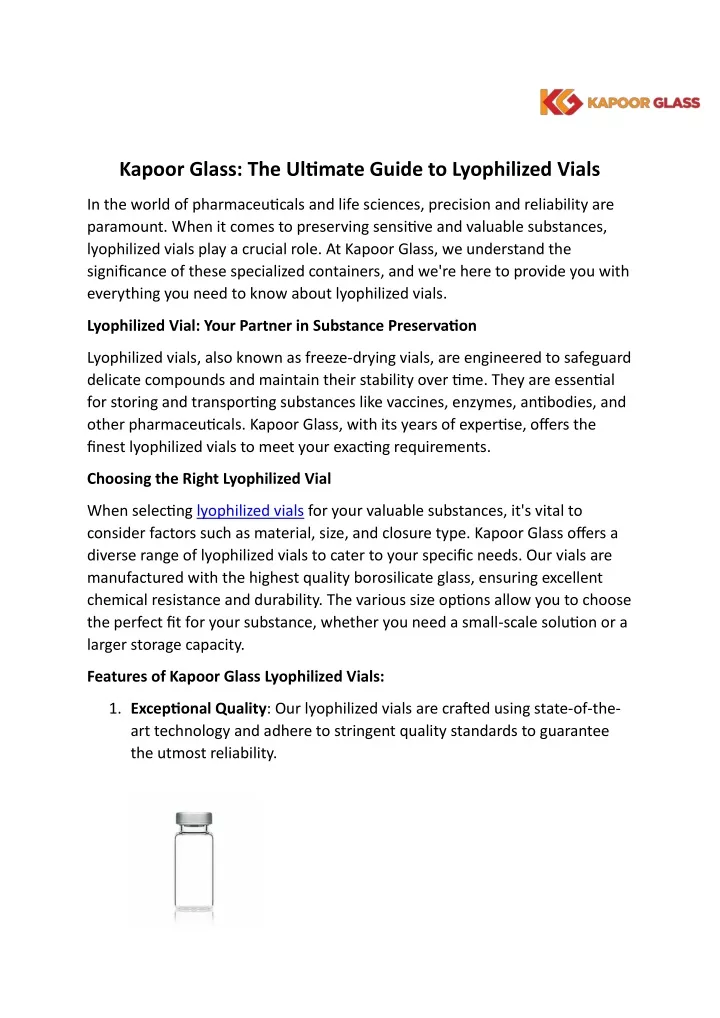
Featured Posts
-
Sydney Mc Laughlin Levrone Breaks 400m Hurdle Record At Miami Grand Slam
May 12, 2025 -
Lily Collins Stars In A New Calvin Klein Campaign See The Photos
May 12, 2025 -
Holstein Kiels Fight Against Relegation A Draw Against Mainz Keeps Champions League Hopes Alive
May 12, 2025 -
Ice Arrest Citizen Intervention And Subsequent Disturbances
May 12, 2025 -
Chantal Ladesou Reconnait L Autruche De Mask Singer 2025
May 12, 2025