Overcoming Hurdles In Automated Visual Inspection Of Lyophilized Drug Products
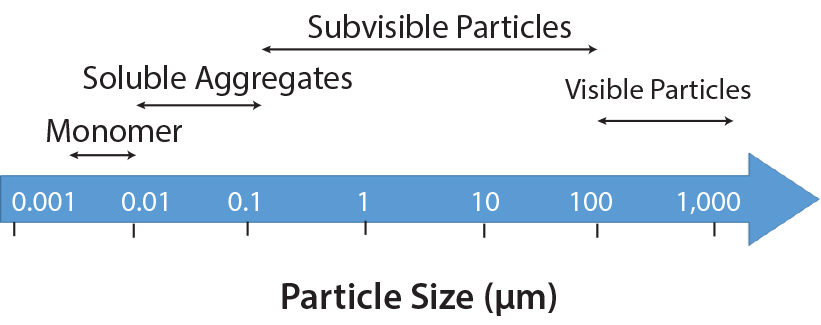
Table of Contents
Challenges in Image Acquisition for Automated Visual Inspection
The first major hurdle in implementing automated visual inspection systems for lyophilized drugs lies in the complexities of image acquisition. Variations in product appearance and the high-throughput requirements of pharmaceutical manufacturing present significant obstacles.
Variations in Lyophilized Product Appearance
Lyophilized drug products exhibit considerable variability in their visual characteristics, making consistent automated inspection challenging. These variations directly impact the effectiveness of image analysis algorithms.
- Different formulations lead to variations in color, texture, and surface characteristics. A formulation change can drastically alter the appearance of the final product, requiring adjustments to the inspection parameters.
- Sublimation patterns vary significantly. The process of lyophilization itself leaves unique patterns on the product surface, which can be misinterpreted as defects if not properly accounted for in the algorithms.
- Cracks, fissures, and other defects can be subtle and difficult to detect. The resolution and sensitivity of the imaging system are crucial for identifying these minor imperfections.
- Lighting inconsistencies can affect image quality. Uneven lighting can create shadows and reflections, obscuring defects and leading to inaccurate inspection results.
The impact of these variations necessitates robust image preprocessing techniques. Algorithms must be trained on a diverse dataset representing the full range of expected variations in appearance to ensure accurate defect detection. For instance, variations in the color of the drug substance itself (e.g., due to different batches of raw materials) need to be accommodated, necessitating sophisticated color correction algorithms within the automated visual inspection system.
High-Throughput Requirements
Pharmaceutical manufacturing demands high-throughput processing. Automated visual inspection systems must be capable of inspecting a large number of vials quickly and efficiently to keep pace with production demands.
- Automated systems need to inspect a large number of vials quickly and efficiently. This requires high-speed imaging capabilities and optimized vial handling mechanisms.
- High-speed imaging and sophisticated algorithms are critical. The system needs to capture high-resolution images at a rate that doesn't compromise accuracy.
- System downtime needs to be minimized for optimal throughput. Regular calibration and maintenance are essential to minimize interruptions and maximize productivity.
Balancing speed and accuracy is a significant challenge. Increasing the speed of image acquisition can reduce the overall inspection time, but it can also decrease image quality and consequently reduce the accuracy of defect detection. Efficient vial handling and transport mechanisms are, therefore, critical components of a successful automated visual inspection system, minimizing bottlenecks and maximizing throughput.
Developing Robust Image Analysis Algorithms
The development of robust and accurate image analysis algorithms is another critical hurdle in automated visual inspection of lyophilized drugs. These algorithms must be capable of reliably detecting and classifying a wide range of defects while minimizing false positives and negatives.
Defect Detection and Classification
The algorithms used in automated visual inspection systems must be highly sensitive and specific to accurately identify various defects.
- Algorithms need to reliably identify a wide range of defects (cracks, particulate matter, discoloration, etc.). This requires sophisticated algorithms capable of discerning subtle variations in texture, color, and shape.
- False positives and false negatives must be minimized. False positives lead to unnecessary rejection of good products, while false negatives allow defective products to pass through.
- Machine learning and AI techniques can enhance accuracy. These techniques allow the algorithms to learn from large datasets of images and improve their performance over time.
- Data augmentation can improve algorithm training. Techniques such as image rotation, scaling, and noise addition can significantly increase the size and diversity of the training dataset.
Convolutional neural networks (CNNs) are particularly well-suited for this application due to their ability to extract features from images and learn complex patterns. However, the effectiveness of these algorithms critically depends on the quality and size of the training dataset. A diverse and representative dataset is crucial to ensure that the algorithms can generalize well to new, unseen samples.
Dealing with Shadows and Reflections
Shadows and reflections are common problems in image acquisition, particularly when dealing with vials of varying shapes and orientations. These artifacts can mask or mimic actual defects.
- Shadows and reflections can obscure defects, leading to inaccurate inspection results. Effective image processing is essential to mitigate this problem.
- Advanced image processing techniques are necessary to compensate. Algorithms are needed to identify and remove or correct shadows and reflections.
- Specialized lighting solutions can improve image quality. Careful control of lighting conditions can minimize the occurrence of shadows and reflections.
- 3D imaging techniques might offer advantages. Three-dimensional imaging can provide more complete information about the product's surface, making it easier to identify defects that might be obscured in 2D images.
Techniques such as shadow removal algorithms and specialized lighting configurations, such as structured illumination, can significantly improve the quality of the acquired images. Exploring 3D imaging modalities offers potential for more robust and accurate defect detection in future systems.
Validation and Regulatory Compliance for Automated Visual Inspection Systems
Regulatory compliance is paramount for any automated system used in pharmaceutical manufacturing. Rigorous validation and adherence to data integrity guidelines are critical aspects of implementing automated visual inspection of lyophilized drugs.
Method Validation
Before an automated visual inspection system can be deployed, it must undergo rigorous validation to demonstrate its accuracy and reliability.
- Rigorous validation is crucial to demonstrate the accuracy and reliability of automated systems. This involves a comprehensive series of tests and analyses to verify that the system meets the required performance specifications.
- Validation protocols must comply with regulatory guidelines (e.g., FDA guidelines). Compliance with relevant regulatory guidelines is essential to ensure the system's acceptance by regulatory authorities.
- Performance metrics (e.g., sensitivity, specificity) must be carefully evaluated. These metrics quantify the system's ability to correctly identify defects and avoid false positives and negatives.
- Comparability to manual inspection must be established. The automated system's results should be compared to those obtained using manual visual inspection to ensure equivalence.
The validation process typically involves several stages, including design qualification, installation qualification, operational qualification, and performance qualification. Comprehensive documentation is required at each stage to demonstrate compliance with regulatory guidelines and to establish the system's reliability and traceability.
Data Integrity and Traceability
Maintaining data integrity and traceability is crucial for regulatory compliance and to ensure the system's overall reliability.
- Maintaining data integrity and traceability is vital for regulatory compliance. This ensures that all inspection data is accurate, reliable, and can be traced back to its source.
- Automated systems must generate auditable trails. This allows for the reconstruction of the inspection process and verification of results.
- Data security is paramount. The system must be designed to protect sensitive data from unauthorized access and modification.
- Integration with existing quality control systems is important. The data generated by the automated system should be seamlessly integrated into existing quality control systems for comprehensive data management.
Secure data storage and access control mechanisms are essential to protect the integrity of the inspection data. The system should also incorporate electronic records and signatures to ensure auditability and compliance with regulatory requirements for electronic data management.
Conclusion
Automated visual inspection of lyophilized drugs offers a significant advancement in pharmaceutical quality control, providing faster, more consistent, and objective assessments compared to manual methods. However, overcoming challenges related to image acquisition, algorithm development, and regulatory compliance is critical for successful implementation. By addressing these hurdles through innovative solutions and collaborative efforts across the pharmaceutical industry and technology providers, we can pave the way for widespread adoption of automated visual inspection, ensuring higher quality and greater safety of lyophilized drug products. Investing in and implementing effective strategies for automated visual inspection of lyophilized drugs is essential for the future of pharmaceutical manufacturing. Consider the benefits of advanced automated visual inspection systems and explore solutions that can improve your lyophilized drug product quality control today.
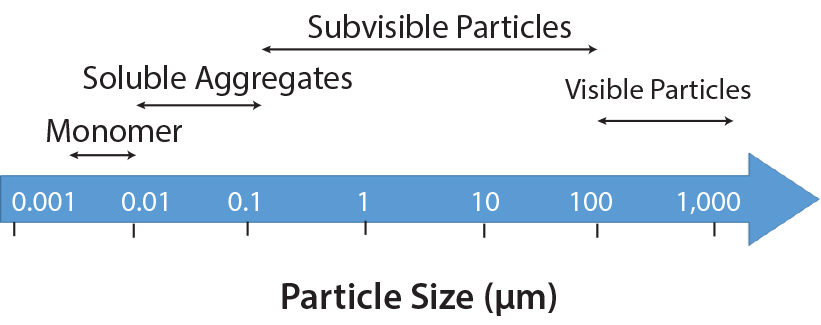
Featured Posts
-
First Look Lily Collins And Charlie Mc Dowells Daughter Tove
May 11, 2025 -
Invest Smart A Map Of The Countrys Rising Business Hotspots
May 11, 2025 -
John Wick Franchise Examining Keanu Reeves Single Portrayal
May 11, 2025 -
Tom Cruise And Ana De Armas Spotted Together Again In England Dating Speculation Intensifies
May 11, 2025 -
Private Credit Jobs 5 Dos And Don Ts For Application Success
May 11, 2025