The Future Of Automated Visual Inspection For Lyophilized Vials
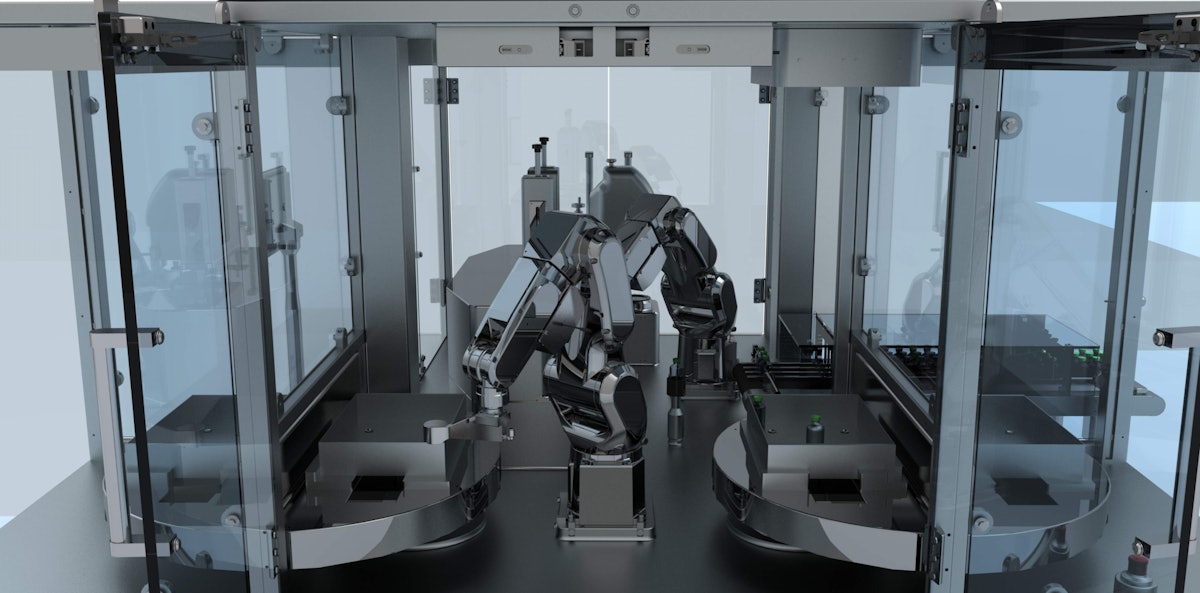
Table of Contents
Advanced Imaging Technologies for Lyophilized Vial Inspection
The foundation of effective automated visual inspection lies in advanced imaging technologies capable of detecting even the subtlest defects in lyophilized vials. These technologies are pushing the boundaries of what's possible in quality control.
High-Resolution Imaging
High-resolution imaging plays a crucial role in detecting critical defects. Employing high-resolution cameras with increased pixel density provides unparalleled detail, enabling the identification of minute cracks, particulate matter, and vial imperfections often missed by the human eye. Advanced lighting techniques, such as darkfield and brightfield illumination, further enhance defect visibility.
- Increased pixel density: Allows for sharper images and the detection of smaller defects.
- Improved sensitivity: Enhanced ability to detect subtle variations in color, texture, and surface features.
- Various lighting options (e.g., darkfield, brightfield): Optimizes contrast and reveals defects that may be invisible under standard lighting.
- Capabilities for 3D imaging: Provides a more complete view of the vial and its contents, facilitating the detection of three-dimensional defects.
Keyword integration: High-resolution imaging, Lyophilized vial inspection, defect detection, pharmaceutical quality control.
Spectral Imaging
Beyond standard high-resolution imaging, spectral imaging offers a powerful tool for identifying contaminants and subtle variations invisible to the naked eye or even standard cameras. This technology analyzes the spectral signature of materials, enabling precise differentiation and the detection of contaminants that might be indistinguishable in visible light.
- Identifying specific materials: Precise identification of materials based on their unique spectral signatures.
- Detecting subtle color variations: Reveals color differences imperceptible to the human eye, indicating potential defects or contamination.
- Enhanced contrast for better defect visualization: Improves the visibility of defects by enhancing the contrast between the defect and its surroundings.
Keyword integration: Spectral imaging, contaminant detection, material identification, Lyophilized vial quality control, pharmaceutical analysis.
Artificial Intelligence (AI) and Machine Learning (ML) in AVI
The integration of Artificial Intelligence (AI) and Machine Learning (ML) is revolutionizing automated visual inspection, significantly improving accuracy and efficiency. These technologies are moving AVI beyond simple defect detection into predictive maintenance and proactive quality control.
AI-powered Defect Classification
AI algorithms, particularly deep learning models, are transforming defect classification. These algorithms analyze images, learn to identify different defect types, and automatically categorize them. This automated process drastically reduces human intervention, improves accuracy, and minimizes false positives.
- Deep learning models: Leverage large datasets of images to learn and classify defects with high accuracy.
- Image recognition: Automated identification and classification of various defects based on learned patterns.
- Automated defect reporting: Generates detailed reports on the types and locations of defects, facilitating timely corrective actions.
- Reduced human intervention: Minimizes the need for manual review, freeing up human resources for other critical tasks.
Keyword integration: AI-powered inspection, Machine learning algorithms, automated defect classification, Lyophilized vial quality, intelligent quality control.
Predictive Maintenance
AI's predictive capabilities extend beyond defect detection to optimize equipment maintenance. By analyzing data from AVI systems and other manufacturing equipment, AI algorithms can predict potential equipment failures, allowing for proactive maintenance and minimizing costly downtime.
- Real-time monitoring: Continuous monitoring of equipment performance to identify anomalies and potential problems.
- Anomaly detection: Identifies deviations from normal operating parameters, indicating potential equipment malfunctions.
- Predictive maintenance scheduling: Predicts equipment failures and schedules maintenance proactively, minimizing downtime.
- Reduced downtime: Proactive maintenance significantly reduces unplanned downtime and maximizes production efficiency.
Keyword integration: Predictive maintenance, AI in manufacturing, automated visual inspection systems, Lyophilized vial production, pharmaceutical equipment maintenance.
Integration and Data Management in Automated Visual Inspection Systems
Effective implementation of AVI systems requires seamless integration with existing production lines and robust data management capabilities. This ensures efficient workflows and provides valuable insights for process improvement.
Seamless Integration with Existing Production Lines
Modern AVI systems are designed for easy integration with existing manufacturing systems and data management systems, streamlining workflows and minimizing disruption. This integration is vital for efficient operation and compliance with industry standards like Industry 4.0.
- Industry 4.0 compliance: Ensures compatibility with modern manufacturing standards and data exchange protocols.
- Data integration capabilities: Seamless integration with existing ERP, MES, and LIMS systems.
- Streamlined workflows: Automated data transfer and reporting, eliminating manual data entry and reducing errors.
- Reduced integration costs: Modern systems are designed for simplified integration, minimizing implementation time and costs.
Keyword integration: System integration, data management, production line efficiency, automated inspection systems, pharmaceutical data integration.
Data Analytics and Reporting
The data generated by AVI systems provides valuable insights into the manufacturing process. Robust data analytics capabilities are essential to leverage this data for process optimization and continuous improvement.
- Real-time data analysis: Immediate access to key metrics, enabling rapid identification and resolution of issues.
- Trend identification: Identifies trends in defect rates and other key parameters, enabling proactive adjustments to the manufacturing process.
- Defect rate tracking: Monitors defect rates over time, allowing for assessment of the effectiveness of quality control measures.
- Process improvement strategies: Data-driven insights enable the development and implementation of strategies to optimize the manufacturing process and reduce defect rates.
Keyword integration: Data analytics, process optimization, quality control metrics, automated visual inspection data, pharmaceutical process improvement.
Conclusion
Automated visual inspection systems are transforming quality control for lyophilized vials. By leveraging advanced imaging technologies, AI, and robust data management, pharmaceutical manufacturers can achieve unprecedented levels of accuracy, speed, and efficiency. The future of automated visual inspection for lyophilized vials involves further integration of AI, improved data analytics, and a shift toward fully automated, closed-loop systems. Embracing automated visual inspection solutions is not just about enhancing quality control; it’s about ensuring patient safety and building a more efficient and reliable pharmaceutical manufacturing process. Consider implementing advanced automated visual inspection systems for your lyophilized vial production today to stay ahead of the curve and ensure the highest standards of quality.
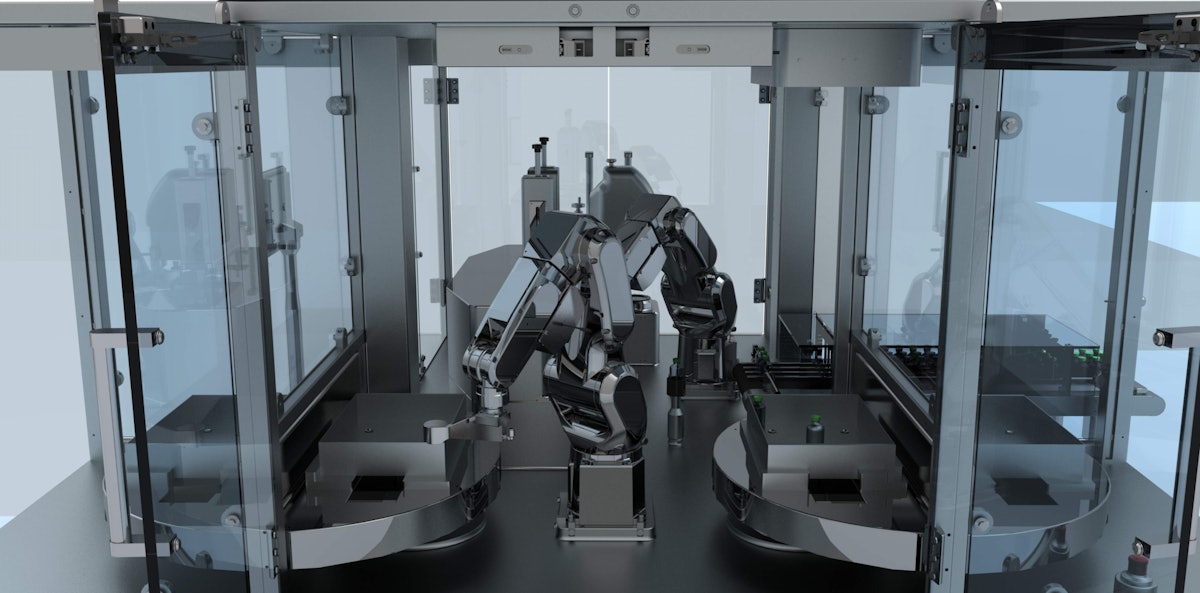
Featured Posts
-
The Next Pope Nine Cardinals Contend For The Papacy
May 11, 2025 -
Selena Gomez And Benny Blanco Wedding Plans The First Dance Debunked
May 11, 2025 -
Yankees Brewers Series Whos On The Injured List March 27 30
May 11, 2025 -
Virginia Giuffres Life Threat After Bus Crash Prince Andrew Case Fallout
May 11, 2025 -
Federal Charges Filed In Massive Office365 Data Theft Case
May 11, 2025