The Future Of Automated Visual Inspection For Lyophilized Vials: Addressing Current Limitations
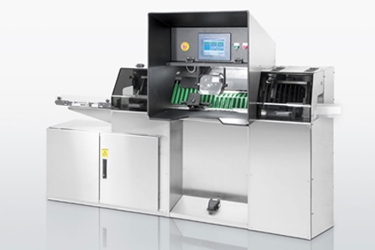
Table of Contents
Current Limitations of Manual Visual Inspection for Lyophilized Vials
Manual visual inspection of lyophilized vials suffers from several significant limitations impacting product quality, efficiency, and cost. Human error is a primary concern, leading to inconsistencies and potential product recalls. The subjective nature of defect classification introduces variability among inspectors, making consistent quality control difficult.
- High Error Rates: Studies show a significant rate of human error in manual inspection, often leading to the release of defective vials.
- Subjectivity and Variability: Different inspectors may classify the same defect differently, resulting in inconsistencies in quality control.
- Low Throughput and High Costs: Manual inspection is a time-consuming process, leading to low throughput and high labor costs, impacting overall production efficiency.
- Difficulty with Complex Defects: Subtle defects like minute cracks, discoloration variations, or particulate matter are often missed during manual inspection.
- Contamination Risk: Manual handling increases the risk of contamination, jeopardizing product sterility and integrity.
Examples of defects frequently missed during manual inspection include:
- Particulate matter within the vial
- Microscopic cracks in the vial's glass
- Slight discoloration of the lyophilized product
- Incomplete lyophilization (e.g., residual moisture)
- Improper seal integrity
These limitations necessitate a shift towards automated solutions for enhanced quality control and efficient production.
Advanced Technologies for Automated Visual Inspection
Advanced technologies are revolutionizing visual inspection of lyophilized vials, offering significant improvements in accuracy, speed, and efficiency.
Machine Vision Systems and AI-powered Defect Detection
Machine vision systems employ high-resolution cameras and sophisticated algorithms to analyze images of lyophilized vials, identifying defects with significantly higher accuracy than human inspectors. The integration of Artificial Intelligence (AI), particularly deep learning and convolutional neural networks (CNNs), further enhances the capabilities of these systems.
- AI-powered algorithms: Deep learning models are trained on large datasets of images, enabling them to learn complex patterns and identify even subtle defects. Examples include YOLO (You Only Look Once) and Faster R-CNN for object detection and classification.
- Superior Accuracy and Speed: AI-powered machine vision systems offer superior accuracy and speed compared to manual inspection, significantly reducing human error and improving throughput.
- Adaptability and Learning: AI algorithms can adapt to variations in lighting, vial orientation, and product characteristics, enhancing the system's robustness and reliability.
High-Throughput Automated Inspection Systems
Automated inspection systems are designed to handle large volumes of vials, significantly increasing throughput and reducing processing time. Robotic handling systems ensure seamless integration with inspection systems, minimizing manual intervention and further reducing contamination risks.
- Increased Speed and Efficiency: Automated systems drastically improve inspection speed, processing hundreds or thousands of vials per hour compared to the limited capacity of manual inspection.
- Reduced Labor Costs: Automation reduces the need for a large workforce dedicated to visual inspection, leading to substantial cost savings.
- Enhanced Production Capacity: Higher throughput allows for increased production capacity without compromising quality control.
3D Imaging and Advanced Lighting Techniques
Moving beyond 2D imaging, 3D imaging techniques provide a comprehensive view of the vial and its contents, allowing for the detection of defects invisible in 2D images. Advanced lighting techniques such as structured light and polarized light further enhance defect visibility.
- 3D Imaging: Provides detailed information about the vial's geometry and the lyophilized product's three-dimensional structure, enabling the detection of defects like subtle cracks or variations in fill volume.
- Specialized Lighting: Structured light and polarized light improve the contrast and visibility of defects, enhancing the accuracy of defect detection.
- Improved Defect Detection: These techniques significantly improve the detection of defects that might be missed using traditional 2D imaging and standard lighting.
Addressing Challenges in Automated Visual Inspection Implementation
Despite the significant advantages, implementing automated visual inspection systems presents some challenges.
Data Acquisition and Algorithm Training
Training AI algorithms requires large, high-quality datasets of labeled images representing various defects. Acquiring and accurately labeling this data can be time-consuming and resource-intensive.
- Data Augmentation: Techniques like data augmentation (e.g., image rotation, scaling) can help increase the size and diversity of training datasets.
- Model Optimization: Fine-tuning AI models and optimizing algorithms is crucial to achieve high accuracy and efficiency.
System Integration and Validation
Integrating automated systems into existing manufacturing workflows requires careful planning and coordination. Validation and regulatory compliance, such as meeting FDA guidelines, are crucial for ensuring the system's reliability and trustworthiness.
- Workflow Integration: Seamless integration with existing manufacturing processes is critical for efficient operation.
- Validation and Compliance: Thorough validation and compliance with regulatory guidelines (e.g., 21 CFR Part 11) are essential.
Cost and Return on Investment
The initial investment in automated visual inspection systems can be substantial. However, the long-term cost savings through increased efficiency, reduced labor costs, and minimized product recalls make the investment worthwhile.
- Cost-Benefit Analysis: Careful consideration of initial investment costs versus long-term cost savings is vital.
- ROI Calculation: Calculating the return on investment (ROI) and payback period helps justify the investment.
Conclusion: The Future is Automated: Embracing Advanced Visual Inspection for Lyophilized Vials
Manual visual inspection of lyophilized vials is limited by high error rates, low throughput, and significant labor costs. Automated systems using AI-powered machine vision, 3D imaging, and advanced lighting techniques offer a significant improvement in accuracy, speed, and efficiency. While implementation challenges exist, addressing these through careful planning and investment in appropriate technologies offers a strong return on investment. Upgrade your visual inspection process; implement automated systems to improve your lyophilized vial quality control and ensure patient safety. Embrace the future of automated visual inspection to gain a competitive advantage and enhance the quality and reliability of your lyophilized products.
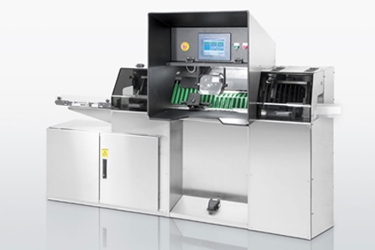
Featured Posts
-
Selena Gomezs Accidental Reveal A Glimpse Into Benny Blancos Private Life
May 12, 2025 -
Exploring The World Of Hotel Transylvania From Movies To Games
May 12, 2025 -
Polemica En La F1 Dijo Un Piloto Argentino Que Uruguay Es Provincia Nuestra
May 12, 2025 -
Jessica Simpsons Snake Sperm Statement Controversy And Reaction
May 12, 2025 -
Exclusif L Avis D Une Legende Tv Sur L Arrivee De Hanouna A M6
May 12, 2025