The Technological Barriers To Robotic Nike Shoe Assembly
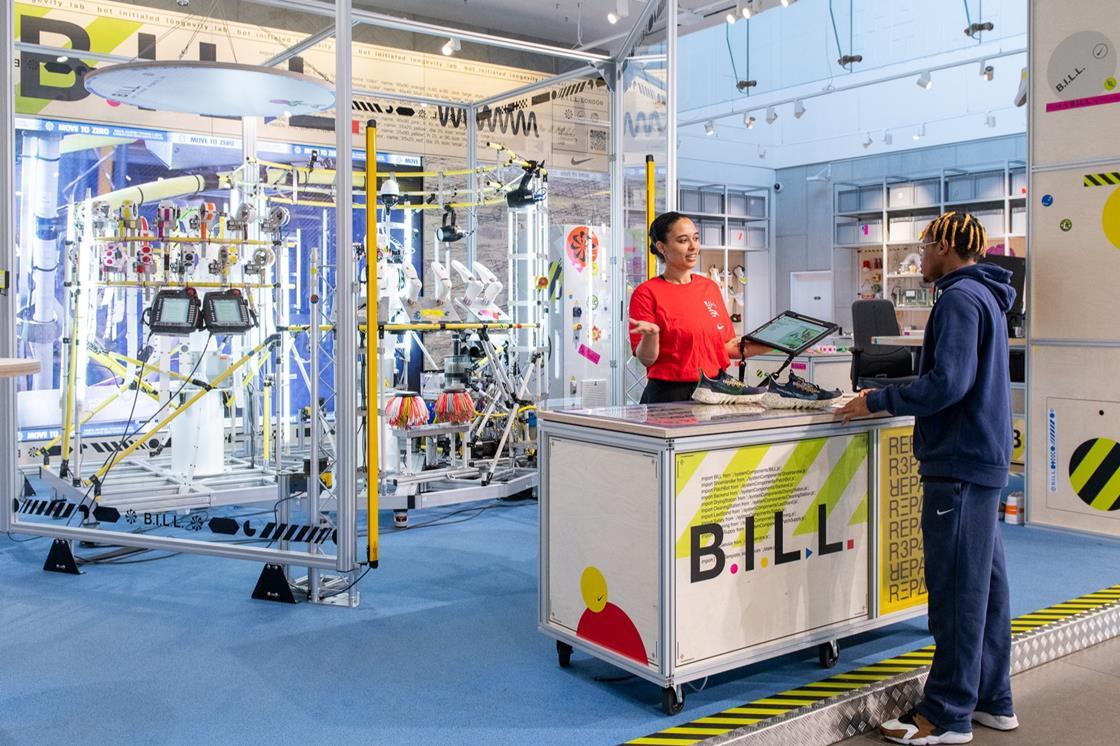
Table of Contents
Dexterity and Precision Challenges in Robotic Shoe Assembly
The intricate nature of shoe construction presents a formidable challenge for robotic automation. Current robotic technology struggles to replicate the dexterity and precision of human hands, particularly when dealing with the varied materials and processes involved in shoe manufacturing.
The Complexity of Shoe Construction
Shoe assembly is a multifaceted process demanding fine motor skills and adaptability. Robots currently lack the nuanced capabilities required for several key steps:
- Precise placement of delicate materials: Applying adhesives precisely, ensuring even stitching, and accurately placing reinforcing materials require a level of precision that's difficult for robots to achieve consistently. Slight misalignments can significantly impact the quality and durability of the finished product.
- Handling various shoe components: Shoe components come in various shapes, sizes, and textures (leather, fabric, rubber, plastics). Robots need to be able to grip and manipulate these diverse components without damaging them. This requires highly adaptable grippers and sophisticated control systems.
- Adapting to variations in materials and designs: Nike produces a vast array of shoe models, each with unique designs and materials. Robots need to be reprogrammable and adaptable to handle these variations efficiently. This requires flexible software and robust AI systems.
Limitations of Current Robotic Grippers
Existing robotic grippers, while improving rapidly, still fall short of the dexterity needed for effective shoe assembly. Several key limitations persist:
- Difficulty gripping soft materials: Soft materials like leather and certain fabrics are difficult for standard grippers to handle without causing damage. The gripping force needs to be carefully controlled to avoid tearing or stretching.
- Inconsistent grasping force: Inconsistent gripping force can lead to dropped components, misalignment during assembly, and ultimately, defective shoes. More sophisticated sensors and control systems are needed to ensure consistent and reliable grasping.
- Lack of adaptability: Current grippers often lack the adaptability needed to handle the diverse range of shoe parts and sizes. Developing grippers capable of adapting to various shapes and sizes is crucial for widespread robotic adoption.
Software and Programming Hurdles
Beyond the physical limitations of robots, significant software and programming challenges hinder the automation of shoe assembly. Developing robust AI capable of handling the variability and complexities of this process is critical.
Developing Robust AI for Shoe Assembly
Programming robots to perform the numerous steps in shoe assembly demands highly sophisticated AI capable of handling unexpected situations and adapting to variations.
- Advanced computer vision systems: Robots need accurate computer vision to identify and locate components within a potentially cluttered workspace. The AI must be robust enough to handle variations in lighting and component orientation.
- Algorithms for complex manipulation tasks: Tasks like threading, knotting, and intricate stitching require sophisticated algorithms that can handle the complex dynamics of these operations. This represents a major challenge in AI development.
- Software for efficient adaptation to new designs: Nike constantly introduces new shoe designs. The software controlling robotic assembly lines needs to be easily reprogrammable and adaptable to these new designs, minimizing downtime and reprogramming efforts.
Integration Challenges with Existing Manufacturing Lines
Integrating robots into existing Nike factories presents significant logistical and operational challenges.
- Adapting existing assembly lines: Existing assembly lines will need to be significantly modified or redesigned to accommodate robotic systems. This is a costly and time-consuming process.
- Training human-robot collaboration: Successful integration necessitates training human workers to collaborate effectively with robotic systems. This includes understanding safety protocols and troubleshooting potential issues.
- Managing integration disruptions: Integrating robots into an active manufacturing environment is inherently disruptive. Careful planning and execution are vital to minimize downtime and maintain production efficiency during the integration process.
Cost and Economic Factors
The high initial investment and uncertainties surrounding the return on investment (ROI) present significant economic barriers to widespread robotic adoption in Nike shoe production.
High Initial Investment Costs
The initial capital expenditure required for robotic automation is substantial:
- Cost of advanced robotic arms: Robotic arms with the necessary dexterity and precision are expensive. The cost increases with the required degrees of freedom and advanced sensors.
- Expense of AI development and implementation: Developing and implementing the sophisticated AI systems needed for robust robotic control and adaptation is a costly undertaking.
- Infrastructure modifications and worker retraining: Modifying existing factories to accommodate robotic systems and retraining workers are additional significant expenses.
Return on Investment (ROI) Uncertainty
The economic viability of robotic shoe assembly depends on a positive ROI. However, several uncertainties exist:
- Long-term cost-benefit analysis: A thorough cost-benefit analysis is necessary to justify the significant investment in robotic automation. This analysis should consider long-term operational costs and potential productivity gains.
- Uncertainties around productivity gains: While robotic automation promises increased productivity, the actual gains might be lower than initially projected due to unforeseen challenges and downtime.
- Risk of technological obsolescence: Rapid technological advancements mean that robotic systems could become obsolete relatively quickly, requiring costly upgrades and replacements.
Conclusion
While the vision of robotic Nike shoe assembly offers significant potential benefits, substantial technological barriers remain. From the dexterity challenges of handling complex components to the development of sophisticated AI and the high initial investment costs, numerous obstacles need to be overcome. Further research and development in robotics, AI, and related fields are crucial to making fully automated Nike shoe production a reality. Overcoming these technological barriers to robotic Nike shoe assembly will require sustained innovation and significant investment, but the potential rewards for efficiency and cost reduction are considerable. Let's continue pushing the boundaries of automation to achieve this ambitious goal.
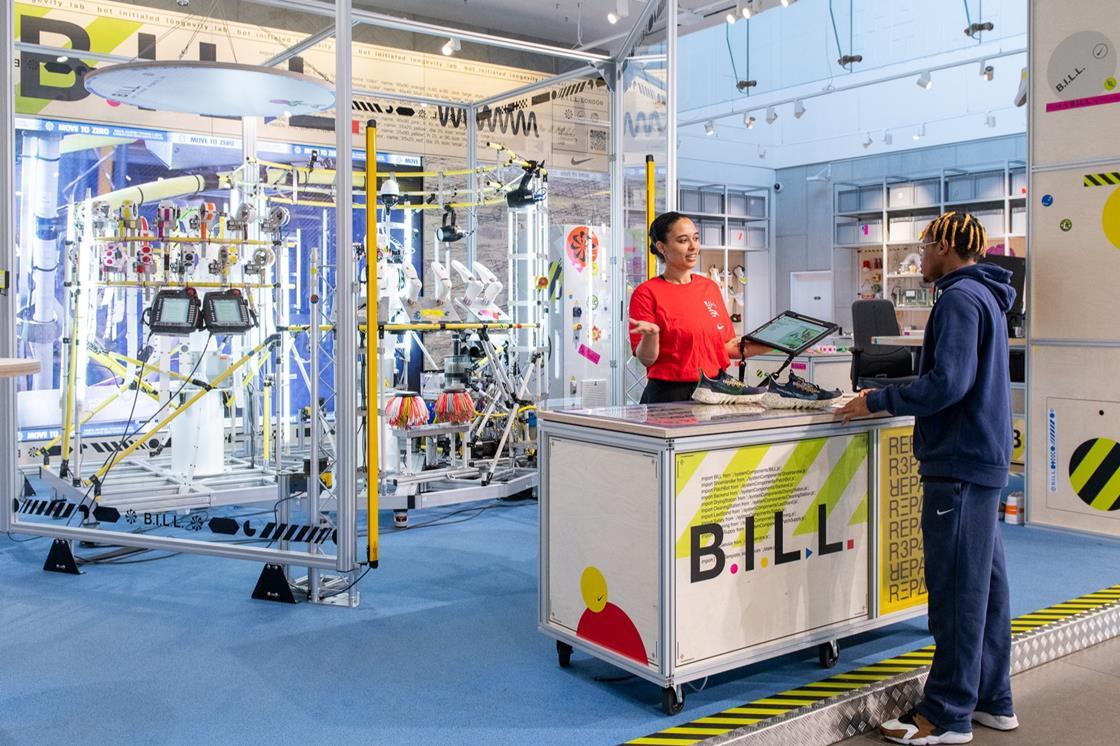
Featured Posts
-
Long Term Effects Of Ohio Train Derailment Toxic Chemical Contamination Of Buildings
Apr 22, 2025 -
Actors Join Writers Strike A Complete Shutdown Of Hollywood Production
Apr 22, 2025 -
High Stock Market Valuations A Bof A Analysis For Investors
Apr 22, 2025 -
Russias Easter Truce Ends Renewed Fighting In Ukraine
Apr 22, 2025 -
Who Will Pay For Trumps Economic Policies
Apr 22, 2025